Keeping your truck or fleet on the road doesn’t just depend on driving skill—it starts long before the engine is turned on. Whether you’re an owner-operator managing one vehicle or a fleet manager overseeing dozens or even hundreds of trucks, an organized maintenance schedule helps avoid costly breakdowns, improve safety, and increase vehicle lifespan.
A well-structured truck maintenance plan is a core requirement for regulatory compliance. Agencies like the Department of Transportation (DOT) and Federal Motor Carrier Safety Administration (FMCSA) require commercial vehicles to be regularly inspected and maintained to meet safety standards. Failure to comply can result in fines, vehicle downtime, and even being placed out of service.
Maintenance also ties directly into Heavy Vehicle Use Tax (HVUT) compliance, specifically with IRS Form 2290. For example:
- Tracking your truck’s gross weight and usage mileage is essential for accurate tax calculations.
- Staying on top of inspections ensures your truck remains in the correct taxable category and helps avoid the need for 2290 amendments (like weight increases or mileage exceeded).
- Maintaining accurate Vehicle Identification Numbers (VINs) through regular inspections can help avoid registration delays or IRS rejections.
In this guide, we’ll walk through a step-by-step approach to creating a truck maintenance plan that not only keeps your vehicles in peak condition but also helps you stay fully compliant and prepared for audits, filings, and renewals.
What Is a Truck Maintenance Plan?
A truck maintenance plan is a structured and strategic schedule designed to ensure that your truck—or entire fleet—is regularly inspected, serviced, and repaired. This plan outlines the frequency, type, and scope of maintenance activities needed to keep vehicles operating safely and efficiently. It serves as a roadmap to reduce the risk of breakdowns, avoid costly emergency repairs, and meet all regulatory compliance requirements.
Purpose of a Truck Maintenance Plan
A solid maintenance plan is more than just a to-do list—it’s a vital component of your business operations. Its core purposes include:
- Maximizing Uptime: Avoid unexpected mechanical failures that lead to costly delays and lost revenue.
- Improving Safety: Ensure brakes, tires, lights, and steering systems are always in safe working condition to reduce the risk of accidents.
- Extending Vehicle Life: Regular service and part replacements help prevent wear and tear, allowing trucks to stay in service longer and perform better.
- Staying Compliant: Meet federal and state regulations from the DOT, FMCSA, and IRS (such as Form 2290 HVUT requirements), and avoid violations during inspections or audits.
Types of Truck Maintenance
To develop an effective plan, it’s important to understand the types of maintenance that apply to commercial vehicles:
1. Preventive Maintenance
- Definition: Scheduled servicing based on time, mileage, or hours of operation.
- Examples: Oil changes, brake inspections, fluid top-offs, tire rotations.
- Goal: Address issues before they cause breakdowns or lead to compliance problems.
2. Predictive Maintenance
- Definition: Maintenance based on real-time data and vehicle condition, often powered by sensors and telematics.
- Examples: Monitoring engine temperature or oil condition to predict when service is needed.
- Goal: Prevent failures by acting on early warning signs using technology.
3. Corrective Maintenance
- Definition: Repairs made after a fault or issue has already occurred.
- Examples: Replacing a failed alternator or fixing a broken air compressor.
- Goal: Restore the vehicle to working condition, though often more expensive and disruptive than preventive action.
4. Scheduled vs. Unscheduled Maintenance
- Scheduled Maintenance: Tasks performed at set intervals (e.g., every 15,000 miles). These are part of your routine truck maintenance plan.
- Unscheduled Maintenance: Unplanned repairs due to unexpected breakdowns. These typically result in higher costs and downtime.
By combining these different maintenance types into a cohesive plan, trucking businesses can create a system that anticipates issues, avoids unnecessary repairs, and ensures every truck meets operational and regulatory standards.
Step-by-Step Guide to Creating a Truck Maintenance Plan
Creating an effective truck maintenance plan doesn’t need to be complicated, but it does require structure, consistency, and attention to detail. The following step-by-step guide will help you build a plan that keeps your trucks road-ready and compliant.
Step 1: Inventory Your Fleet and Equipment
Start by compiling a complete inventory of your vehicles and any equipment that needs regular maintenance.
- Log Key Details: Record each truck’s make, model, year, VIN (Vehicle Identification Number), current mileage, axle configuration, and load capacity.
- Track Maintenance History: If possible, gather historical maintenance records to understand what’s already been done and identify recurring issues.
- Include Equipment: Don’t forget to inventory trailers, refrigeration units, liftgates, and any other operational gear that requires upkeep.
A clear inventory lays the foundation for customizing service intervals and tracking ongoing maintenance needs.
Step 2: Review Manufacturer Recommendations
Refer to each vehicle’s OEM (Original Equipment Manufacturer) manual to find baseline maintenance guidelines.
- Use OEM Service Intervals: These typically include mileage- or time-based suggestions for servicing critical components like the engine, brakes, transmission, and cooling systems.
- List Required Inspections and Replacements: Note which parts should be inspected, replaced, or serviced routinely—such as belts, filters, fluids, and spark plugs.
Manufacturer guidelines are a great starting point for building your custom service intervals.
Step 3: Set Service Intervals
Now that you know what needs attention, determine when each service task should occur.
- Use Multiple Schedules:
- Daily/Pre-trip: Basic visual inspections.
- Weekly: Fluid top-offs, tire pressure checks.
- Monthly: Battery checks, lights, hoses.
- Mileage-Based: Oil changes every 15,000 miles, tire rotations every 30,000 miles, air filter replacement every 45,000 miles.
- Daily/Pre-trip: Basic visual inspections.
Service intervals should be tailored to each truck’s usage—heavily used trucks may need more frequent maintenance.
Step 4: Develop an Inspection Checklist
Create standardized checklists to ensure thorough, consistent inspections across all vehicles.
- Key Items to Include:
- Safety Components: Brakes, tires, lights, mirrors, wipers.
- Mechanical Systems: Engine, suspension, driveline.
- Fluids & Filters: Oil, coolant, transmission, fuel, air filters.
- Cab/Interior Checks: HVAC, electrical, seat belts, dashboard indicators.
- Safety Components: Brakes, tires, lights, mirrors, wipers.
Include both pre-trip and post-trip inspection requirements. Make sure drivers are trained to identify and report issues immediately.
Step 5: Assign Responsibilities
Clearly define who is responsible for performing, reviewing, and recording maintenance tasks.
- Drivers: Perform daily pre and post-trip inspections, report issues.
- Technicians/Mechanics: Conduct scheduled maintenance and repairs.
- Supervisors/Managers: Monitor reports, ensure compliance, approve major repairs.
Training your staff ensures consistency and builds accountability into the process.
Step 6: Choose a Recordkeeping System
Accurate documentation is essential for compliance, tax filing, and performance analysis.
- Paper Logs vs. Digital Tools: While paper can work, digital fleet maintenance software is more efficient and reliable.
- Integration with Technology: Use systems that integrate with telematics, GPS, and ELDs (Electronic Logging Devices) for automatic tracking of mileage, engine hours, and fault codes.
ExpressTruckTax customers often benefit from using digital logs when filing 2290 returns or claiming HVUT credits.
Step 7: Schedule Maintenance and Track Compliance
Proactively schedule all service events in advance using digital calendars or fleet management tools.
- Automated Alerts: Use software to send reminders based on mileage or date.
- Prioritize Preventive Work: Address small issues before they become larger, costlier problems.
- Link to Regulatory Requirements: Align your schedule with DOT and IRS compliance needs (such as weight category monitoring for 2290 filings).
Consistent scheduling reduces emergency repairs, boosts uptime, and ensures vehicles are legally road-ready.
Step 8: Monitor and Adjust the Plan
A maintenance plan shouldn’t be static—it must evolve based on real-world performance.
- Review Data Regularly: Use service logs and diagnostics to identify patterns, recurring failures, or changes in wear rates.
- Quarterly or Bi-Annual Reviews: Set times to review and refine your plan based on vehicle usage, mechanic feedback, and inspection outcomes.
- Adapt to Business Changes: If you add new vehicles, change routes, or shift workloads, update your plan accordingly.
Staying flexible ensures the plan continues to meet operational and regulatory needs as your business grows.
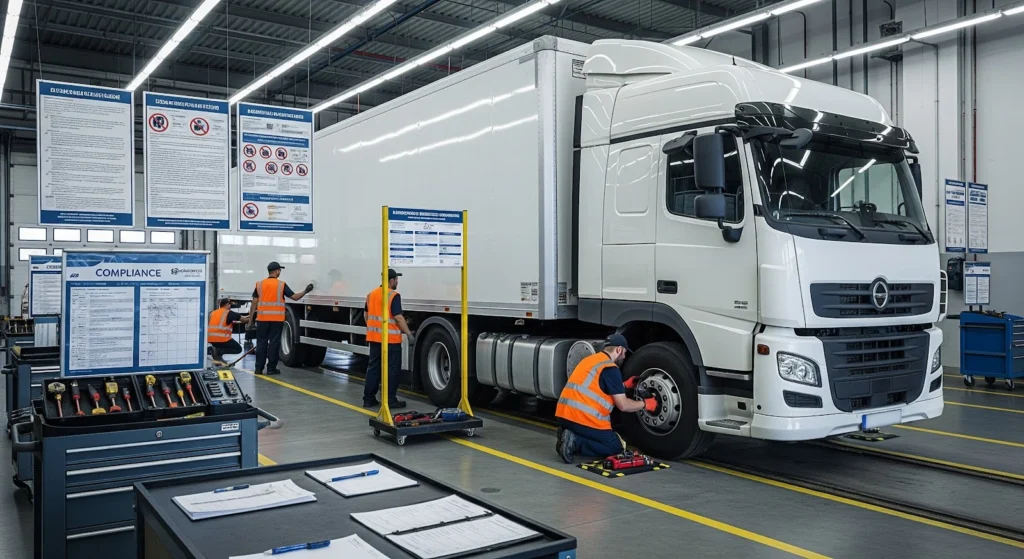
Compliance and Documentation
A truck maintenance plan does more than protect your vehicle—it protects your business from legal, financial, and operational setbacks. Ensuring your maintenance records are accurate, complete, and accessible is critical for passing inspections, avoiding penalties, and staying compliant with state and federal regulations.
Maintain Logs for DOT Audits and Inspections
The Department of Transportation (DOT) and Federal Motor Carrier Safety Administration (FMCSA) require commercial motor carriers to maintain comprehensive maintenance records for each vehicle. These records may be reviewed during:
- Roadside inspections
- DOT safety audits
- Compliance reviews
- Investigations following accidents
To stay compliant, you should maintain:
- Driver Vehicle Inspection Reports (DVIRs) – pre-trip and post-trip
- Service records – detailing every oil change, brake job, and repair
- Parts replacements
- Odometer readings – to track service intervals and validate tax filings
- Proof of corrective actions – for any issues found during inspections
DOT regulations require these records to be kept for at least 12 months while the vehicle is in use, and six months after it’s retired. Digital logs are not only easier to maintain but also simplify retrieval during time-sensitive audits.
How a Truck Maintenance Plan Supports HVUT Filings (Form 2290)
Maintenance records play a key role in helping you file IRS Form 2290 accurately and efficiently. Here’s how:
- VIN Accuracy: Regular inspections help ensure Vehicle Identification Numbers (VINs) are correctly recorded—eliminating costly mistakes on your 2290 return.
- Gross Weight Monitoring: Staying on top of suspension, load-bearing components, and upgrades helps you properly classify the vehicle’s taxable weight category.
- Mileage Limit Tracking: If your truck was initially filed as “suspended” (under 5,000 miles or 7,500 for agricultural use), a maintenance plan combined with mileage logs helps identify when you’ve exceeded the limit—prompting a 2290 mileage amendment.
- Claiming Credits (Form 8849): If a vehicle was sold, destroyed, or retired during the tax year, maintenance logs serve as supporting documentation for claiming HVUT credits using Form 8849 Schedule 6.
Your maintenance plan becomes a built-in tool for ensuring HVUT compliance, reducing the risk of IRS rejections, and avoiding DMV registration delays due to incorrect or outdated filings.
Keep Documentation Organized for DMV or Tax Purposes
Well-organized records are essential not just for audits and taxes, but also for:
- Title and registration renewals with your state’s Department of Motor Vehicles (DMV).
- Proving roadworthiness during weigh station checks or law enforcement stops.
- Insurance claims, especially after accidents or equipment failures.
- Tax deductions and depreciation calculations, supported by your maintenance and usage records.
Tips for organization:
- Use digital recordkeeping platforms with cloud backup.
- Store all service receipts, inspections, and logs by VIN.
- Keep a separate folder for each vehicle’s compliance documents.
- Integrate with software like ExpressTruckTax to streamline tax records, VIN corrections, and 2290 amendments.
By building documentation into your maintenance routine, you’re not just staying compliant—you’re creating a paper trail that protects your business, simplifies filings, and keeps your trucks on the road without unnecessary regulatory setbacks.